James Alexander Corporation has established an extensive Quality Assurance program that is designed to meet all of the requirements of the Food and Drug Administration for both drug products and medical devices.
James Alexander’s Quality Assurance program includes the following elements:
Facility maintenance and pest control programs
Equipment calibration program traceable to NIST standards
An extensive CGMP & QSR compliant training program for production and quality assurance personnel
Internal audit program conducted by QA personnel
Guidelines and requirements for independent testing laboratories contracted by James Alexander Corporation
Process validation studies
Preventive maintenance procedures for equipment and machinery
Stability test program for James Alexander stock medical products
Documented procedures for handling customer complaints
Corrective and Preventive Action Program
Continuous Process Improvement through a Total Quality Management program
Semi-annual Executive Management Review of important quality issues
All manufacturing procedures at James Alexander Corporation are conducted in accordance with established procedures designed to assure stock medical products of the highest quality and purity. In fact, all products produced by James Alexander pharmaceutical or not, are manufactured to these same high standards.
Current Good Manufacturing Procedures include the following systems:
Thorough review of product specifications by James Alexander Engineering and Quality Assurance personnel to assure that all specifications can be consistently met
Establishment of Master Files in order to document product history
Strict segregation and identification of incoming raw material components pending inspection and release by Quality Assurance
Segregation of non-conforming raw material components in a designated quarantine area
Comprehensive Supplier Qualification and Monitoring program to assure that all raw material components meet established specifications
Document control system to assure that our Quality Assurance and Process Documentation is current and that any revisions are thoroughly documented
Line clearance procedures carried out by trained Quality Assurance personnel prior to beginning any manufacturing or processing procedure
- Clear and unequivocal labeling of released raw material components present in manufacturing and processing areas to prevent mix-up or cross-contamination
- Performance and documentation of in-process quality control checks to assure compliance with product specifications
Use of equipment and processes that have been thoroughly tested and validated by Quality Assurance
Maintenance of traceability from receipt of raw materials to shipment of final product through accurate and detailed documentation
Yield reconciliation calculations for each manufacturing run to assure product potency and purity
Quality Assurance inspection and, when applicable, analytical testing carried out prior to release of finished product
Environmental monitoring of critical manufacturing areas
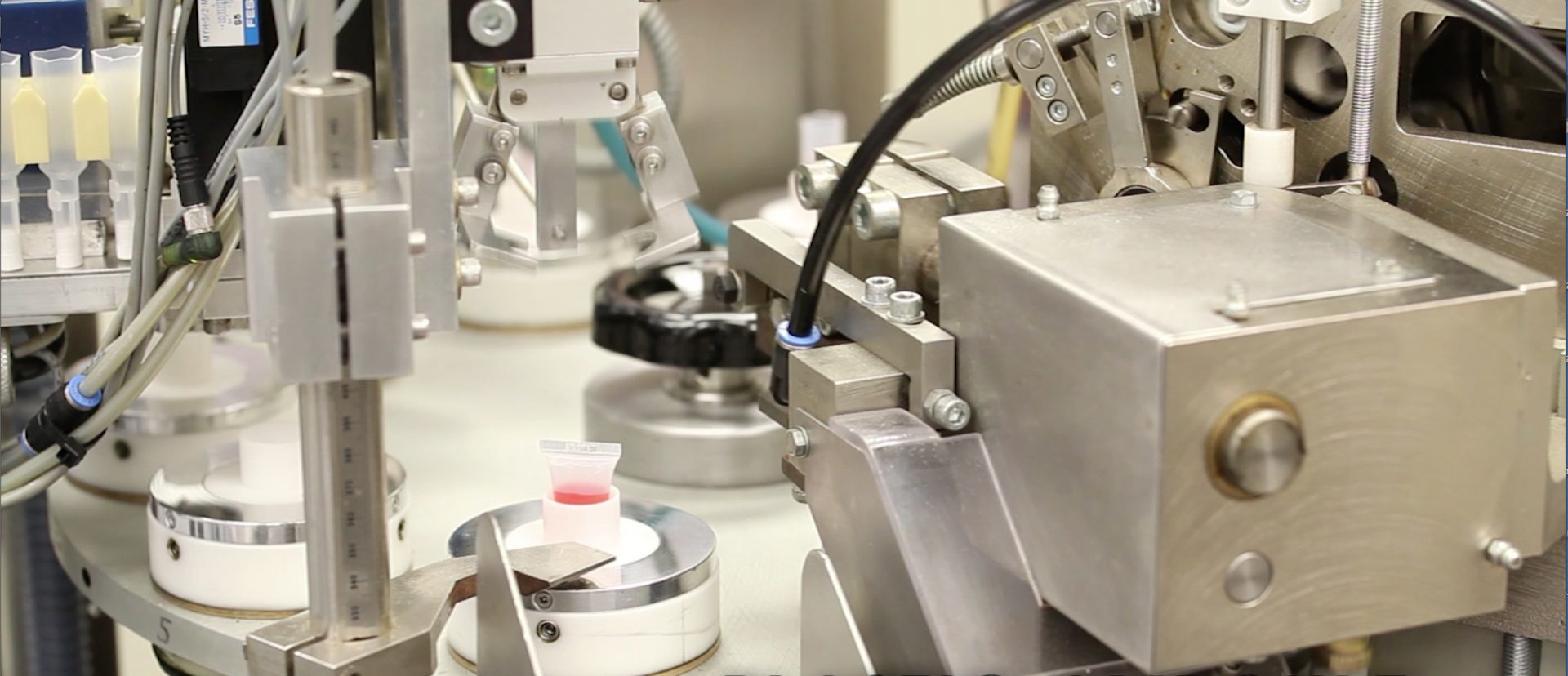
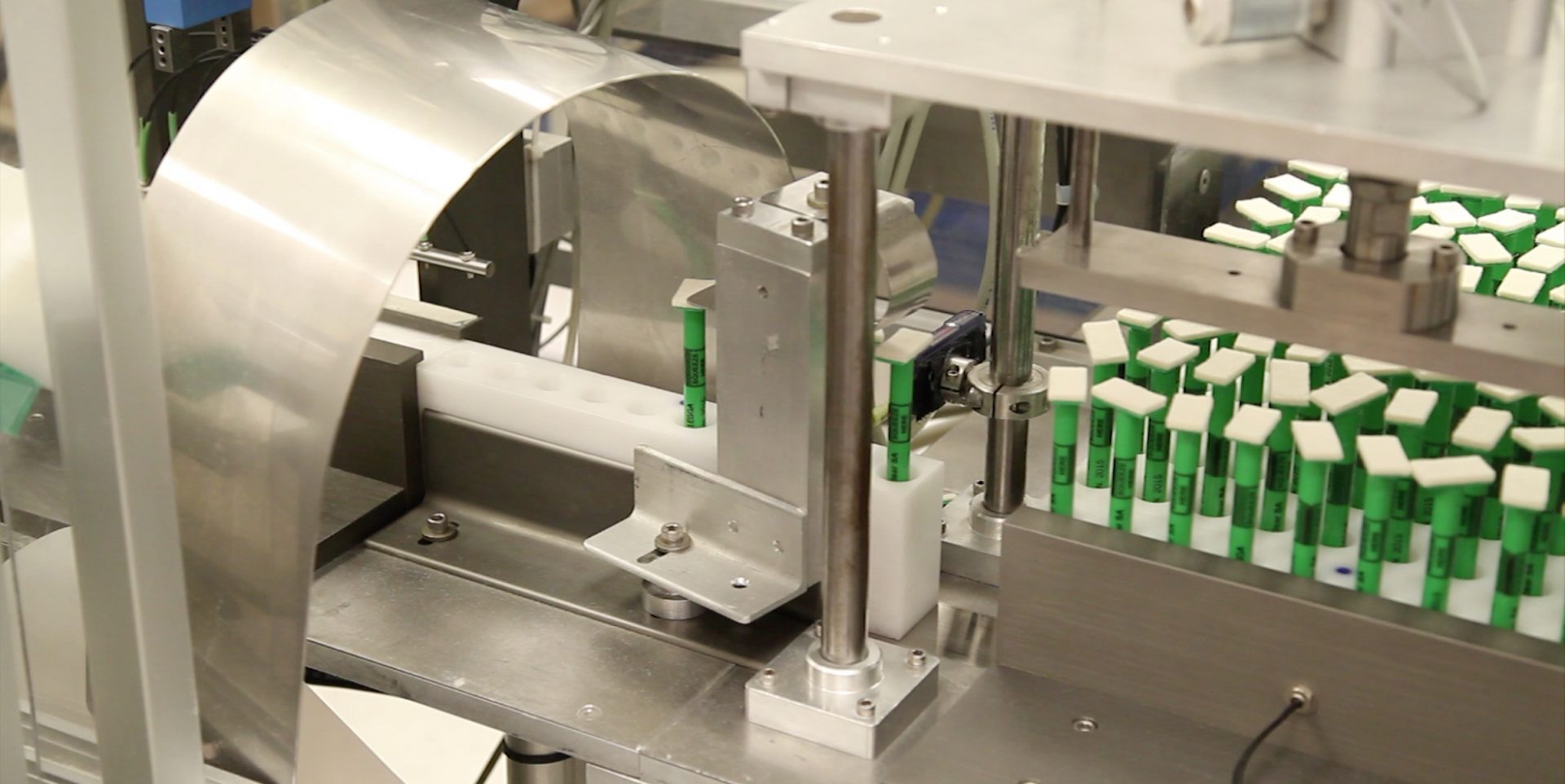
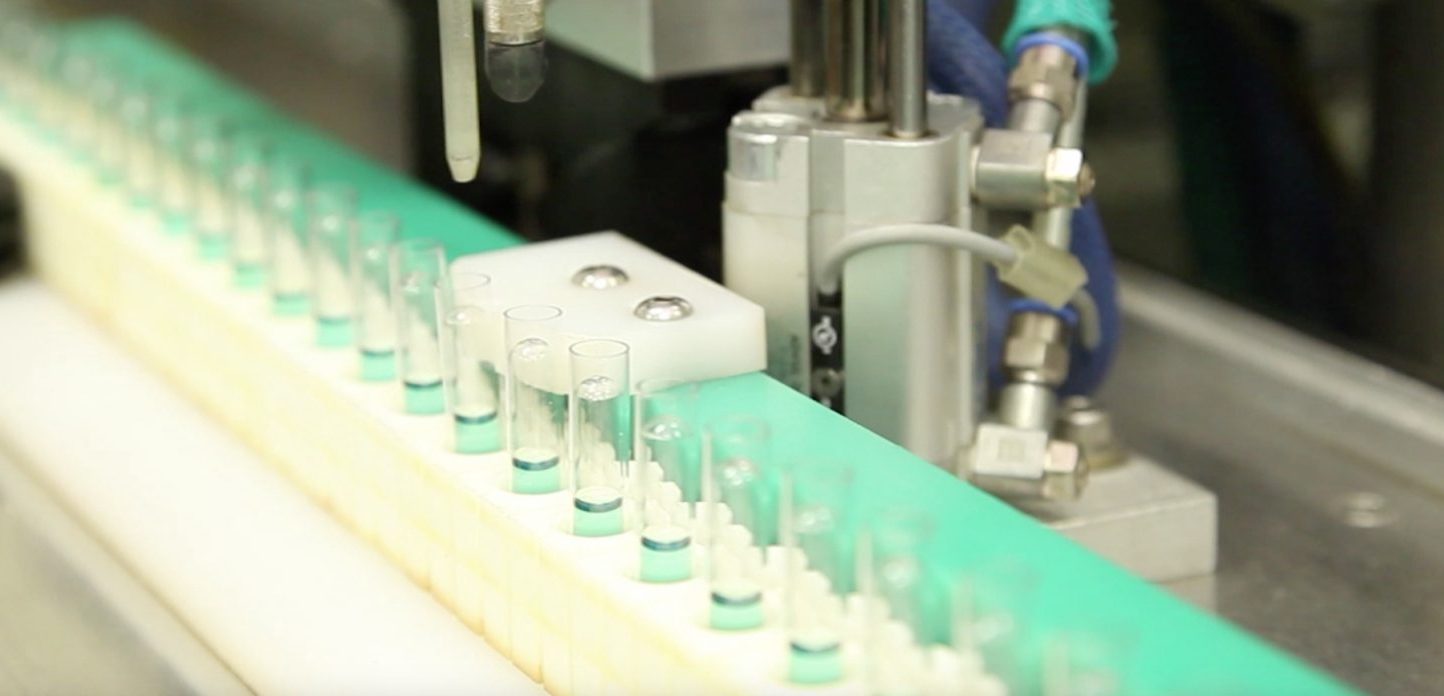
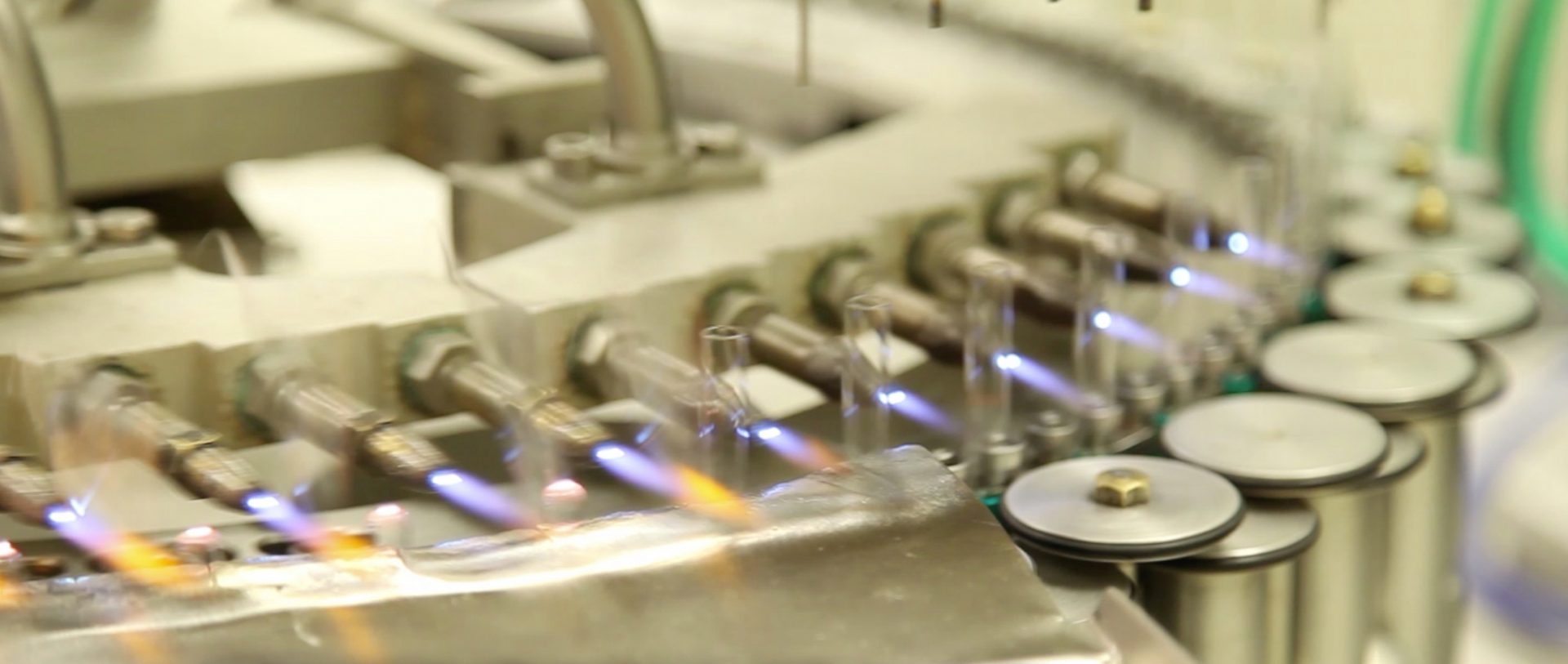